
Incremental sheet forming
Incremental sheet forming for rapid prototyping
Van-Cuong Do, Xiao-Xiao, Young-Suk Kim*
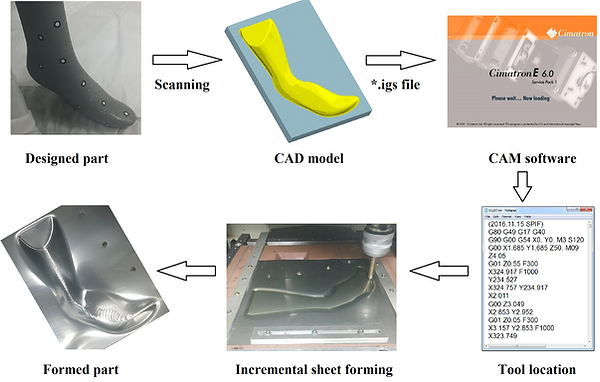
Introduction
- Incremental sheet forming (ISF) uses one small hemispherically ended tool moving along a predefined toolpath to locally deform a completely clamped sheet of metal such that the total sum of the local deformations contributes to the final desired shape of the sheet.
- ISF is flexible forming method to make parts of varying shapes such as conical, pyramidal shape, complex shape, automotive part…
- ISF shows advantages in comparison with stamping method as following
: cheaper machine and die investment, flexibility.
Forming limit curve in ISF
- ISF is limited by fracture with suppression of necking.
- The forming limit curve at fracture (FLCF) is a line from the equi-biaxial strain point to plane strain point and very high in comparison with those in conventional press forming

FLCF in ISF
- Plane strain is defined as thickness strain magnitude at pyramidal shape wall

-Equi-biaxial strain is defined at the centre area of four-wing-star toolpath

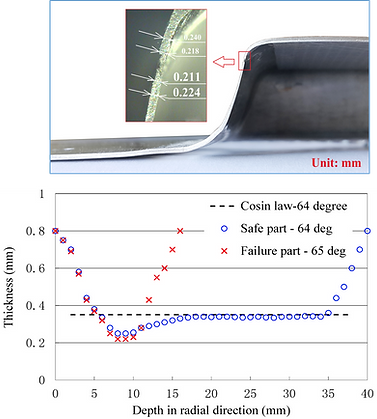
Thickness distribution along
cross-section of pyramid wall
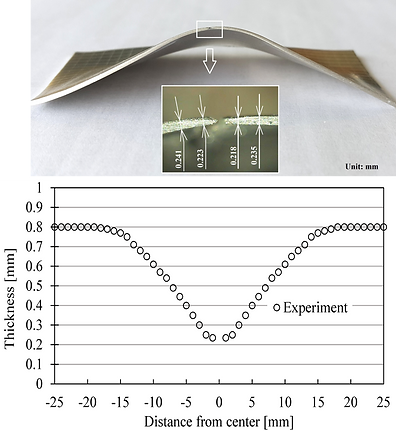
Thickness distribution along cross section
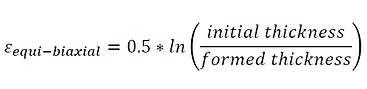
Finite element simulation of ISF
- The ISF is a slow process with cyclic, local plastic strain around tool-sheet contact. The material behaviour should be described by mixed isotropic-non linear kinematic hardening.
- For tested materials, yield function and potential function are different. Non-associated flow rule is applied.
- Material in ISF is deformed until very large strain range, Kim-Tuan hardening equation shows the best fitted stress-strain curve for metal.
- The yield criterion, as function of all state variables, can be written in a generic form as

𝑓𝑦(𝜎−𝛼) is a continuously differentiable yield function; 𝛼 is a backstresstensor in the kinematic hardening model.
𝜎𝑌(𝑝) is work hardening rule which generally represented 3-parameter-Kim-Tuan equation:



아름